Every day we have more and more requests in our catalogue of used machine tools for the purchase of eroding wire cutting machine and eroding die sinking machines.
Today’s question is: what EDM machines are and how does an eroding machine work? What’s the difference between a wire cutting machine and a die sinking machine?
Today we are going to resolve doubts and provide you the right answers
The EDM machine
The electric-discharge or EDM (electric discharge machining) is an important technology, used a lot in the mechanical industry. With this technique you can remove the material by the erosive capacity of electric discharges.
Some info about EDM functioning
First of all, we are going to list the principal characteristics of EDM method:
- Work piece immersed in a dielectric fluid
- Electrode powered by positive polarity
- Piece powered by negative polarity
- Electrode and piece are never in contact (distance: about 25 μm)
- Processing residues: gas and metal spheres (metallic powder type)
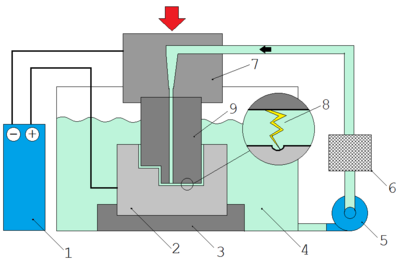
1. Generator of electric discharge 2. Piece (+) 3. Holder 4. Dielectric fluid 5. Pump 6. Fluid 7. Tool holder (-) 8. Discharge 9. Tool
Working phases
- The achievement of a given voltage and the consequent release of electrons from the cathode
- Electron impact with fluid atoms and molecules and the generation of positive and negative ions (chain effect)
- The fluid is completely ionized and becomes a conductor letting the current pass
- The fluid is in the plasma state that cause the melting and the vaporization of certain areas (both of the workpiece and of the tool).
- After the discharge the voltage goes down until it is canceled (drain condensers)
- Condensers restarts to accumulate energy until a tension is reached. In this way the process is triggered again
Die sinking edm
The die sinking machining aims to work the piece by making a complementary form of the electrode. This procedure implies the creation of the negative – electrode (usually a male) instead of the desired one that you need to process.
Wire edm
With this working model, a sparking occurs from the sides of the wire to the work piece, causing erosion.
Drilling by mean of EDM
This application allows the realization of any type of metal piece with diameters of 0.3 up to 6 mm and heights of 300mm and over.
The electric-discharge process
This method utilizes the metal erosion effect that is obtained thanks to innumerable electric discharges generated between the workpiece electrode and the tool electrode.
Discharges start one after the other, creating small holes on the surface of the workpiece.
The discharges generated for long time start to form a regular sequence of holes. In this situation, material will be removed from the surface of the workpiece.
During production between the two electrodes (tool and workpiece) there is a very small gap filled with a special dielectric liquid whose level is maintained constant through an automatic regulation system.
EDM vs traditional removing methods
The chip removal method with EDM instead of traditional ones (turning and milling) has various advantages. Here below some of them:
- No mechanical effort is executed on the workpiece: elimination of the complex locking system
- No constraints associated with uneven wear of the milling cutters ensuring a good precision of the dimensions regardless of the number of pieces to be executed
- Any metal material can be worked (no constraint to its hardness)
- We can create any geometric or volumetric figure
- Excellent working tolerances (±µm)
- High autonomy of machines without operator intervention
There is also some disadvantage
- Less production
- The relative wear of the tool (5/10% of the removed material)
- The surfaces produced with this method always have a certain degree of roughness.
If you are interested in a wire cutting machine or in die sinking machines do not hesitate to consult our on-line catalogue of used machine tools.
If instead you want to sell your EDM machine contact us or you can publish directly your ad! Push the green button here below.